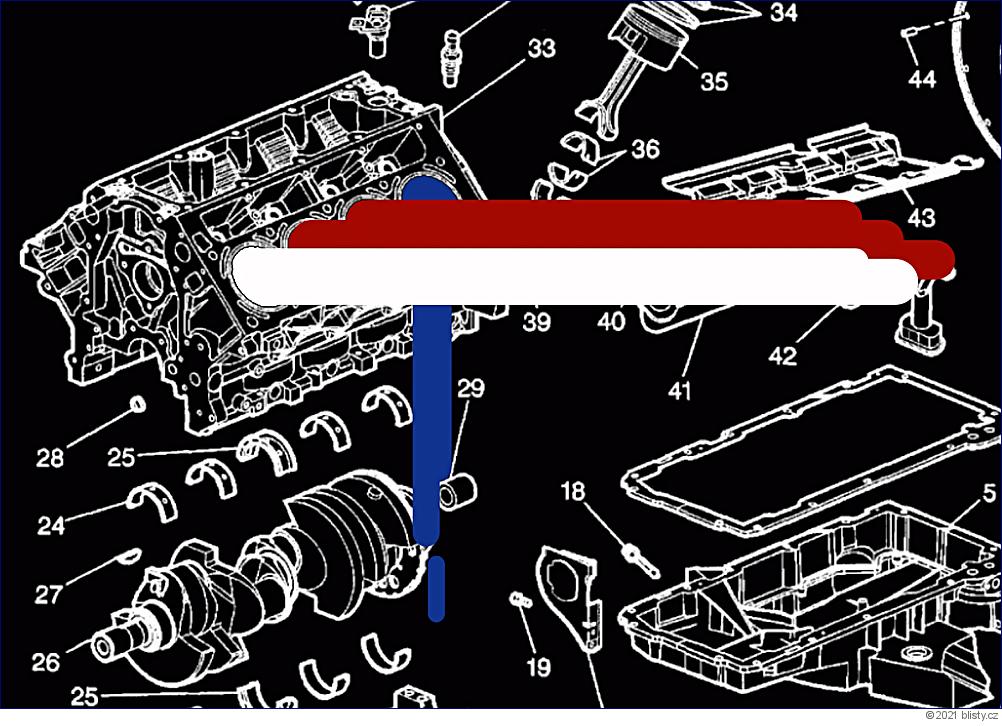
Průmysl 4.0 a virtuální továrny: Výrobci v honbě za novou průmyslovou revolucí využívají digitální dvojníky
18. 8. 2023
Továrna na elektrické holicí strojky v Drachtenu na severu Nizozemska se připravuje na testy, které umožní evropskému průmyslu prosperovat na stále konkurenčnějších mezinárodních trzích. Tato továrna, řízená společností Philips, která se zabývá spotřební elektronikou, se účastní výzkumného projektu financovaného Evropskou unií, jehož cílem je povzbudit výrobce, aby používali digitální dvojníky, jinými slovy virtuální továrny vytvořené pomocí technologií určených k optimalizaci současných výrobních procesů.
Cílem je využít technik, jako je cloud computing, umělá inteligence, robotika a technologie blockchain, k vytvoření modelů výrobních procesů a identifikaci oblastí pro zlepšení. "Průmysl prochází přechodnou fází a digitální technologie mohou pomoci," říká Cécile Girardot, koordinátorka iniciativy DIMOFAC, která potrvá do března 2024: "Digitální dvojníci poskytují data v reálném čase, která mohou ukázat výkon strojů v reálném světě ve virtuální rovině."
Evropský výrobní sektor v hodnotě 5 miliard eur s globálními tahouny v oblastech jako je letectví, ocelářství, automobilový průmysl a chemický průmysl, se musí potýkat s výrobci orientovanými na vývoz v zahraničí a přísnějšími ekologickými normami v rámci Evropské unie. Tyto dvě základní výzvy jsou umocněny prudkým nárůstem cen energií po ruské invazi na Ukrajinu v únoru 2022 a narušením dodavatelského řetězce vyvolaným pandemií COVIDu o dva roky dříve.
EU zřídila partnerství veřejného a soukromého sektoru s názvem Továrny budoucnosti v hodnotě 1,15 miliardy eur na podporu výzkumu a inovací v oblasti výroby, což dokládá význam této otázky v politickém programu EU. V sázce je schopnost evropských společností přizpůsobit se tomu, co bylo nazváno čtvrtou průmyslovou revolucí neboli Průmyslem 4.0, érou charakterizovanou automatizací a konektivitou.
Koncept virtuální továrny se v Evropě stále více prosazuje. Letecká společnost Airbus a specialista na elektrická zařízení Schneider Electric zkoumají koncepty digitálních dvojníků a zakládají virtuální výrobní závody. Od svého uvedení na trh na konci roku 2019 vyvinul DIMOFAC systém pro zefektivnění výrobních procesů zvaný plug-and-produce, který umožňuje rekonfiguraci výrobních linek propojením skutečných strojů s jejich odpovídajícími digitálními dvojníky.
Pomocí tohoto systému může výrobce virtuálně simulovat novou konfiguraci a vyřešit případné problémy online před instalací zařízení do fyzické továrny. Problémy s výrobou mohou nastat například při použití recyklovaných surovin, jejichž vlastnosti nejsou vždy totožné, jak vysvětluje Girardot, která koordinuje evropské projekty v oblasti pokročilých materiálů a výroby ve francouzském výzkumném ústavu CEA-Liten: "V těchto případech je nutné přizpůsobit výrobu. Čím dříve se tak stane, tím lépe. Hlavním cílem je zkrátit čas potřebný pro rekonfiguraci."
Systém plug-and-produce projektu bude pilotně testován v pěti stávajících výrobních závodech po celé Evropě. Vedle elektrických holicích strojků v Nizozemsku existují letecké komponenty vyráběné společností Éirecomposites v Irsku a interaktivní obrazovky vyráběné společností Schaltag ve Švýcarsku. Tato technologie je implementována ve všech pěti lokalitách a výsledky se očekávají během prvního čtvrtletí roku 2024. DIMOFAC se podařilo spojit širokou škálu průmyslových odborných znalostí díky svým 30 partnerům, včetně Siemens Industry Software (Francie), strojírenské společnosti FILL (Rakousko) a EXOM Engineering (Španělsko).
Lepší koordinace navrhování a výroby
Další projekt financovaný EU, FIRST, který posunul budoucnost digitálních továren o krok blíže, zkoumal, jak mohou digitální továrny zvýšit efektivitu výrobních zařízení rozmístěných na více místech. Nové návrhy a procesy vyvinuté společností FIRST posílí spolupráci, řekl Laj Sü, koordinátor iniciativy, která skončila v prosinci 2022 po šesti letech provozu. "V minulosti byly výrobní závody často poměrně izolované," říká Sü, který je také docentem na Bournemouth University (Velká Británie) a pracuje na kolaborativních obchodních procesech a virtuálních podnicích.
Podle Laj Sü se FIRST zaměřil na identifikaci překážek a potíží, které by mohly bránit používání technologií virtuálních továren, a vývoj strategie k jejich řešení. Partnery projektu (celkem sedm) byli výrobci, softwarové společnosti a univerzity a pocházeli ze zemí jako Německo, Itálie, Nizozemsko a Čína. Sü je optimistický ohledně potenciálu, který mohou digitální dvojníci nabídnout průmyslu na obchodní a environmentální úrovni. Například pomocí digitálního modelu celého výrobního procesu by společnost mohla navrhnout pár bot v Paříži nebo Miláně a poté koordinovat jejich výrobu a prodej na globální scéně.
Využitím technologie blockchain by IT síť mohla propojit všechny zúčastněné strany (obchody, designéry, logistické společnosti a výrobce) a zaslat jim informace o tom, co přesně je potřeba, kde a kdy. "Obuv šitá na míru může být navržena na jednom místě a vyrobena na jiném, což vede k efektivnějšímu a flexibilnějšímu výrobnímu procesu a sníženému dopadu na životní prostředí," vysvětluje Sü. Technologie virtuálních továren nevyžadují přístup "všechno nebo nic". Výrobci mohou využít některé aspekty ke zlepšení procesů, aniž by se museli zavázat ke komplexní implementaci. To může být zvláště cenné pro mnoho malých a středních podniků v evropském výrobním odvětví, které nemají zdroje na to, aby zcela přepracovaly své systémy.
Technologie virtuálních továren mohou také pomoci společnostem efektivněji řídit procesy údržby složitých strojů, což vede k úsporám nákladů. "Senzory kolem strojů shromažďují data, která umožňují programování, kdy by měl být vyslán technik, aby je opravil," říká Sü. Jako důkaz stále rostoucího významu virtuálních výrobních technologií koordinátor FIRST říká, že konsorcium hledá finanční prostředky od EU a dalších zemí, aby dosáhlo dalšího pokroku v této oblasti.
Zdroj v angličtině: ZDE
Diskuse